DOD, Army make improvements to PCS process
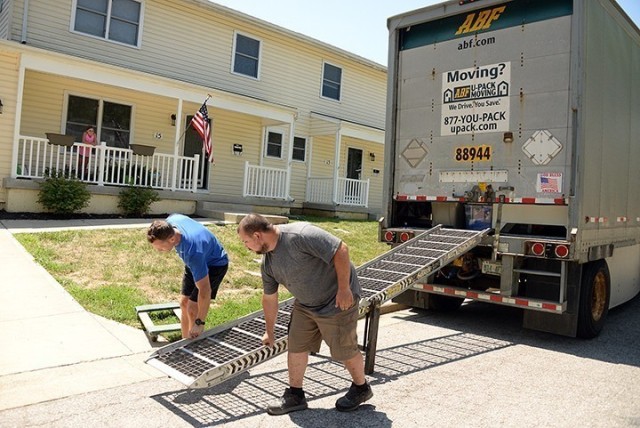
ROCK ISLAND ARSENAL, Ill. — Summer is here and it’s a busy time for U.S. Army personnel and families as they move to their next assignment. Despite domestic improvements regarding COVID-19, the pandemic still proves problematic in other parts of the world and continues to affect the shipping industry.
In response, the U.S. Transportation Command, U.S. Army and the Army Sustainment Command are working hard to continuously improve the permanent change of station process for its customers and family members.
“The pandemic has impacted all sectors of the global market. Ports, port agents, customs, trucking, rail and shipping are all part of those sectors that have been impacted by the pandemic, and they continue to see shortfalls in labor, drivers, material, fuel, increased operating costs as well as other operational resources,” said Col. Courtney Abraham.
Abraham serves as the director of the Army Personal Property Lead Element — or APPLE — and commander of ASC’s Joint Personal Property Shipping Offices-Mid Atlantic, or JPPSO-MA.
Located at Fort Belvoir, Virginia, APPLE is the Army’s lead integrating organization in the Defense Personal Property Program and the collective Joint Enterprise. Its mission is to plan, manage and provide technical oversight to Army Personal Property Shipping and Processing Offices globally.
APPLE maintains operational control of both JPPSOs located at Fort Belvoir and Joint Base Lewis-McChord, Washington. JPPSO-MA is one of six Army-led shipping offices. This organization executes personal property movement services to authorized personnel within a specified area of responsibility. The JPPSO-MA supports shipments within portions of 12 states, including the Washington, D.C. area.
This PCS season brings many improvements compared to previous years, said Abraham. USTRANSCOM has adjusted domestic and international transit times to provide better predictability and expectation management for Soldiers and families for delivery of their household goods, he said.
“All overseas PCS locations could be impacted, no one greater than another,” Abraham said. “The Personal Property enterprise continues to monitor changes in the global supply chain closely and continually communicates with our industry partners in order to implement the best business practices to support our Soldiers and families.”
In late 2020, ASC began equipping units with tablets specifically to aid quality assurance inspectors in the field. “Quality assurance inspectors can perform operations and reporting while on the road, utilizing their WiFi-enabled tablets, mobile devices or hotspots,” Abraham explained.
Tablets allow inspectors to reach more customers in the duty day, as well as to immediately provide customers with resources, handouts and report findings into the USTRANSCOM system of record without having to return to a traditional office.
Additionally, the Army has a 75% onsite physical inspection standard by quality assurance personnel, surpassing the Defense Transportation Regulation standard of 50%. The Army currently has an 87% physical inspection rate, meaning an inspector has provided in-person representation at time of pack, pickup or delivery.
Abraham detailed the following changes to the overall PCS process that have been implemented since May 2021:
- Improving inventories: “We are working with the moving companies to shift from paper copies of inventories and use electronic inventories to the greatest extent possible. This will provide an improved record of the household goods pack-out and the condition they were in when packed. This effort is to accelerate the inventory and accountability process of household goods, eliminate paper copy exchanges, and enable digital transmission and storage of the inventory records offering better services to members and families when moving. Electronic inventories will be mandatory in 2023.”
- Pickup date choice: “[We] refined how Soldiers and families input their desired pickup dates, adding the ability for them to pick a preferred day inside their requested seven-day pickup window. Also known as ‘spread dates,’ this refers to the seven-day window during which your moving company is required to pick up your shipment. This policy is designed to give you more control over requesting a specific date range to schedule your move.”
- Moving company contact: “The moving company will identify points of contact and email the Soldier/family with that information to facilitate better communication before, during and after the move, improving the overall PCS experience.”
- Simplifying claims: “Created a standardized form to simplify filing an inconvenience claim across the DOD. Additionally, military claims offices will be able to declare a catastrophic loss of a shipment regardless of the percent of inventory items lost, damaged or destroyed. In the past, the threshold was 60% of the total shipment.”
- Securing property: “Moving companies are already required to place seals on containers, but we’re adding a requirement that customers be notified if any seals are broken, that seals be replaced, and that these actions and communications are noted in the record.”
- Better communication: “Increased service provider availability by phone – added Saturday customer support requirement during peak of the relocation period; provider must return calls on same business day and wait times cannot exceed 20 minutes. Additionally, movers are required to provide customers a 24-hour notice of delivery and make two attempts to contact the customer, with each attempt at least six hours apart, before transferring the customer’s shipment to storage-in-transit.”
- More control and choice for customer: “More time to file a claim — was 75 days, now 180 days. Simplified convenience claims processing; improved in-transit visibility; single point of contact with moving companies; and have choice to repair or receive repair costs for damages, including full replacement cost.”
- Personally Procured Moves: Formerly known as DITY — Do-It-Yourself moves — reimbursement increased to 100% of what it would have cost the government to use a DOD moving company.
- Inconvenience claims: “Reimbursement up to seven days of per diem and incidentals when a moving company fails to pick-up or deliver as agreed.”
- SmartVoucher process reduces travel payments to less than two days.
- The Basic Allowance for Housing rate is in effect at all 40 on-base Intercontinental Hotel Groups Army Hotel locations in the U.S. through the end of fiscal 2022.
- IHGs have agreed to only charge Soldiers at their BAH rate when they must stay in temporary lodging for extended periods of time due to housing or household good delivery challenges.
- MILPER Message 22-0045(CAC-enabled): Allows commanders the flexibility to change report dates by 30 days either before or after the initial report date, or up to 60-day deferment working with the Installation Directorate of Human Resources to get approval.
Despite all these improvements and bearing aforementioned challenges in mind, Abraham said the Soldier still has much input regarding how successful a PCS can be. He recommended Soldiers always do the following to ensure their PCS goes as smooth as possible:
- Once orders are received, visit the installation transportation office immediately to receive household goods counseling and complete shipment application(s).
- Communicate challenges with chain of command early, so they can assist and work with the installation transportation office to identify all possible options to support the Soldier and their family; there are several choices available to Soldiers and families to support challenges during their PCS Move.
- Provide feedback via the Customer Satisfaction Survey. As of May 15, all customers are now asked to complete a brief survey via text message regarding various milestones throughout their move — entitlement counseling, pack/pickup, delivery and claims.
Resources for PCS Moves
- My Army PCS app offers information on entitlements, types of moves, planning, scheduling, and the claims process with a live chat feature and is available for free download in the Google Play Store and Apple App Store.
- PCS My POV helps you track your vehicle during shipment and is available for free download in the Google Play Store and Apple App Store.
- Army’s Digital Garrison app helps you explore all the benefits your Army post has to offer such as restaurants, events, shops, clinics, activity centers, and directorates. Navigate to on-post facilities, stay updated on local weather, and be informed about gate closures or other important installation information in real time, all from the palm of your hand. It’s available for free download in the Google Play Store and Apple App Store.
- Military One Source: The USTRANSCOM one-stop shop for personal property information and access to systems
- USTRANSCOM Customer Facing Dashboard: Provides customers visibility of individual TSP performance.
- Army Virtual Call Center: Available at 800-521-9959; offers extended customer support hours of operation, additional chat capability and access to 24/7 support through USTRANSCOM.
RELATED STORIES
- October 14, 2022 Army announces new 2022 Cloud Plan
- April 4, 2022 Army seeks Soldier feedback on navigating parenthood while serving
- May 8, 2020 Changes to the Army Talent Alignment Process 21-01 Winter Move Cycle
- February 10, 2020 Army aggressively moves forward on OMFV, seeks industry input on path forward
- March 20, 2017 PCS Week offers info for a successful PCS move
- April 29, 2014 U.S. Army STAND-TO! | DOD's Privately Owned Vehicle Shipping program